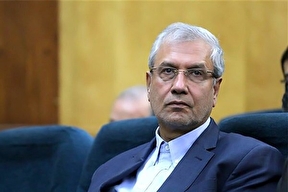
به گزارش خبرگزاری برنا در اصفهان؛ داریوش رشیدی در این باره گفت: با اتکا به دانش فنی و تجربۀ نهادینهشده در فولاد مبارکه و همت شرکتهای سازندۀ داخلی ۲۲ 10 عدد تیوب این ریفورمرها بومیسازی و با موفقیت مورد بهرهبرداری قرار گرفت.
وی با تأکید بر اهمیت کیفیت این تجهیزات تصریح کرد: بسیاری از لولههای وارداتی از رده خارج شده است و با کسب این موفقیت، در حال حاضر حدود یکچهارم ریفورمرهای احیا با لولههای ساخت داخل عملیات تولید را انجام میدهند و تاکنون عملکرد مناسبی داشتهاند.
رشیدی با اشاره به مزایای بومیسازی تیوبهای ریفورمر احیا مستقیم اظهار داشت: با توجه به قیمت زیاد این قطعات و همچنین پرمصرف بودن آنها در شرکت، خرید این تیوبها ارزبری بسیار زیادی به دنبال دارد، اما با بومیسازی این قطعات، علاوهبر اینکه سالانه به میزان 7.6 میلیون یورو صرفهجویی ارزی برای کشور حاصل شده است، با همکاری شرکتهای سازندۀ داخلی در فرایند تولید آنها، موفق به کسب دانش فنی و تکنولوژی ریختهگری سوپرآلیاژها به روش گریز از مرکز و در مقیاس صنعتی در کشور شدهایم.
در ادامه محمدرضا فتحی رئیس واحد احیا مستقیم نیز افزود: لولهها و تیوبهای ریفورمر یکی از قطعات مهم و استراتژیک و دارای بیشترین هزینۀ مالی در واحدهای احیا مستقیم است که فرایند شکست گاز متان و تبدیل آن به گازهای احیایی موردنیاز در دمای بیش از ۱۱۰۰ درجه جهت احیای گندلۀ اکسایدی در آنها انجام میگیرد. خوشبختانه با رویکرد مدیریت فولاد مبارکه در زمینۀ بومیسازی و حمایت همهجانبۀ این شرکت از سازندگان داخلی، در این خصوص کارگروهی با حضور کارکنان متخصص و باتجربۀ شرکت تشکیل شد و با همکاری شرکتهای سازندۀ داخلی، بومیسازی این قطعات فوق حساس مورد بررسی و تبادلنظر قرار گرفت و نهایتا عملیات بومیسازی طی مراحل مختلف انجام شد.باید در نظر داشته باشیم که در برخی پارامترها، در نمونۀ وارداتی امکان بهرهبرداری در بعضی دماها وجود نداشت که در نمونۀ بومیسازیشده این محدودیت برطرف شده است. بدون شک این مهم که هم رهایی از وابستگی و هم جلوگیری از خروج ارز را در پی داشته میسر نشده، مگر به لطف خداوند و با تلاش و اعتماد به توان داخلی که مایۀ مباهات است.
از حوزۀ تعمیرات واحدهای احیا نیز مجتبی کریمی کارشناس تعمیرات اظهار داشت: در سالهای گذشته، تیوبهای ریفورمر احیا بهصورت کامل توسط سازندۀ خارجی تأمین میشد که ضمن ارزبری زیاد، عدم امکان تأمین با توجه به شرایط تحریم نیز یک تهدید بالقوه برای واحدهای احیا مستقیم محسوب میگردید.
خوشبختانه با سرمایهگذاری بخش خصوصی جهت ساخت قطعه و همکاری مستمر بین سازنده، تعمیرات احیا و واحد بومیسازی شرکت، مشکلات فرایند ساخت و تأمین در داخل کشور رفع گردید و در حال حاضر قطعات ساختهشده بهصورت 100 درصد بومی در ریفورمرهای واحد احیا مستقیم نصب شده و در مقایسه با قطعات خارجی، عملکرد مطلوبی از لحاظ پارامترهای فنی مانند خزش و عمر مفید دارد.
در همین خصوص یوسف یلمه تکنسین قطعات یدکی احیا مستقیم گفت: در ریفورمرهای واحدهای احیا مستقیم جمعا تعداد 4068 عدد تیوپ ۱۰ و ۸ اینچ در حال کار است. این تیوبها بهصورت عمودی در کوره نصب و درون آنها از کاتالیستهایی با مشخصات موردنظر پر میشود. گاز طبیعی با عبور از بین لایههای کاتالیست به گازهای احیا شکسته میشود و آمادۀ فرایند احیای گندلهها و تبدیل آنها به آهن اسفنجی میگردد. قبلا این تیوبها با صرف زمان و ارز بسیار زیاد از شرکتهای آلمانی، ژاپنی و اسپانیایی تأمین میشد ولی الآن قطعات بومیسازیشده در زمان بسیار کوتاه و با قیمت غیرقابل مقایسه با انواع وارداتی تحویل میشوند.
در خصوص فرایند بومیسازی این تجهیزات، مسیب فروغی رئیس واحد بومیسازی فولاد مبارکه نیز خاطرنشان کرد: فرایند بومیسازی این قطعات از سال 89 شروع شد. با رفع مشکلاتی که بر سر راه بومیسازی این قطعات بود، خوشبختانه تولید این تیوبها در داخل کشور به بار نشست و پس از طی مراحل تست عملکردی گرم، تاکنون 1022 عدد از این تیوبها توسط شرکتهای داخلی، ریختهگری، ماشینکاری و تحویل شرکت فولاد مبارکه شده است.
با توجه به فقدان تکنولوژی ریختهگری گریز از مرکز سوپرآلیاژها در داخل کشور و همچنین اطلاعات مربوط به متریال و فرایند ریختهگری آنها، ابتدا با تخریب یک نمونه از این تیوبها و انجام فرایند مهندسی معکوس، حیطۀ آنالیز شیمیایی، خواص مکانیکی و ریزساختار مناسب برای این قطعات مشخص شد. پس از آن با همکاری قسمتهای مرتبط اطلاعات مناسبتری در زمینۀ استانداردهای تحویلگیری مناسب برای این تیوبها جمعآوری و تدوین شد.
حسین ایزدی کارشناس واحد بومیسازی نیز در این باره گفت: بهطورکلی این تیوبها از سه قسمت پایینی، بالایی و فلنچ تشکیل شده که متریال هریک از این قسمتها با توجه به دمای اطراف آنها در کوره، طراحی و ساخته میشود. هریک از این قسمتها با استفاده از دستگاههای اتوماتیک جوشکاری پلاسما و یا فرایند جوشکاری GTAW و با استفاده از جوشکاران بسیار متبحر به یکدیگر اتصال مییابند.
در حین فرایند تولید و پس از آن نیز تستهای مختلف اعم از آنالیز شیمیایی، کشش، خزش، ماکروگرافی، متالوگرافی، پنوماتیک و هیدرواستاتیک، مایع نافذ (PT)، رادیوگرافی (RT) زبریسنجی و بروسکوپی بر روی قسمتهای مختلف این تیوبها و با توجه به الزامات مدرک فنی، صورت میپذیرد.
این تیوبها در معرض درجه حرارت بسیار زیاد (1100 درجۀ سانتیگراد) خزش، خوردگی و رسوب کربن قرار دارند و توجه به عمر زیادی که از آنها انتظار میرود، باید از سوپر آلیاژهای با مقادیر بالای نیکل، کروم و دیگر عناصر آلیاژی ازجمله تنگستن، نیوبیوم و تیتانیوم ساخته شوند تا ریزساختار و خواص مکانیکی مناسب را داشته باشند و در دمای کاری خود حداقل به مدت 10 سال استفاده شوند.
در پی کسب این موفقیت داریوش رشیدی مدیر ناحیۀ آهنسازی از تمامی همکاران تولید، تعمیرات، دفاتر فنی واحد احیا مستقیم، خرید قطعات یدکی و ماشینآلات، کنترل کیفیت قطعات یدکی، مهندسی قطعات و تجهیزات و دیگر همکارانی که در این پروژه همکاری داشتهاند تشکر و قدردانی کرد.